rfunk
Well-known member
Took my engine to an old-timer machinist recommended by local garden/lawn tractor shop. Ordered piston as advised, brought to him and had him fit it to the bored and honed cylinder. He also lapped the connecting rod mating surface a couple thou', as it was out-of-round vertically, but on-spec horizontally. I do recall an old engineering prof "engine guy" mentioning doing this. Anyone here heard of it, and, if so, what is your experience with doing this?
During reassembly, (hadn't really gotten around to cleaning up parts properly, before), I saw this:
Cracking?? around spark plug hole. Does not seem to go through head. Is this just a casting defect, or should I be ordering a new head?
I had intended to replace the balance gears, changed my mind after Digger gave me a call, but the shim washers he sent me came in handy anyway: they're the right size for adjusting the camshaft endplay, too.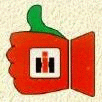
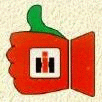
Made sure I checked the ring end gaps, too, my machinist repeated that lots . . .
Planned on doing the Dave Kamp mod on my driveshaft, went from PO's massacre:
to this:
Machine shop said it was easier just to make a new adapter. They'd made it just a bit oversize to go into the drive cup, so chucked the shaft end into my drill press, and gave it a couple light swipes with a file while turning. PERFECT!
Had the machine shop cross-drill the yokes, too, then used the yoke hole to line up and drill the shaft.
Yeah, much larger yokes than I'd like. Doesn't leave much room for the cooling fan. (to be ordered).
Last point of note, the old machinist showed me a crack in the deck, which he said shouldn't be an issue, as it was not up to the valve insert:
Again, comments/experience?
I've had to reassemble my engine with these known defects, because it's my WORKER. After I gave it a 10 minute run-in, I changed the oil and re-torqued the head bolts, then mowed for a couple hours. Not exactly what I'd like to have done, but noted "no" oil used, where before I rebuilt it, I'd have been down more than half a quart, and had the breather slimed up with oil drool. Hoping it stays together, don't want to waste the effort, but figured if the head lets go, at least that is an easy replacement.
Things I'd do differently if I did it again, may do yet, would be adding a larger air filter with an extension, based on the old machinist's comments that the very sandy ("potato growing") soil in my area tends to wear out Kohlers faster than more clayey soils in other, nearby areas. I'd also do some painting and other cleanup, but the grass just won't hold off that long. Maybe next year . . . sigh.
During reassembly, (hadn't really gotten around to cleaning up parts properly, before), I saw this:

Cracking?? around spark plug hole. Does not seem to go through head. Is this just a casting defect, or should I be ordering a new head?
I had intended to replace the balance gears, changed my mind after Digger gave me a call, but the shim washers he sent me came in handy anyway: they're the right size for adjusting the camshaft endplay, too.
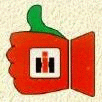
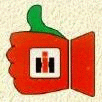
Made sure I checked the ring end gaps, too, my machinist repeated that lots . . .
Planned on doing the Dave Kamp mod on my driveshaft, went from PO's massacre:

to this:


Machine shop said it was easier just to make a new adapter. They'd made it just a bit oversize to go into the drive cup, so chucked the shaft end into my drill press, and gave it a couple light swipes with a file while turning. PERFECT!

Had the machine shop cross-drill the yokes, too, then used the yoke hole to line up and drill the shaft.

Yeah, much larger yokes than I'd like. Doesn't leave much room for the cooling fan. (to be ordered).
Last point of note, the old machinist showed me a crack in the deck, which he said shouldn't be an issue, as it was not up to the valve insert:

Again, comments/experience?
I've had to reassemble my engine with these known defects, because it's my WORKER. After I gave it a 10 minute run-in, I changed the oil and re-torqued the head bolts, then mowed for a couple hours. Not exactly what I'd like to have done, but noted "no" oil used, where before I rebuilt it, I'd have been down more than half a quart, and had the breather slimed up with oil drool. Hoping it stays together, don't want to waste the effort, but figured if the head lets go, at least that is an easy replacement.
Things I'd do differently if I did it again, may do yet, would be adding a larger air filter with an extension, based on the old machinist's comments that the very sandy ("potato growing") soil in my area tends to wear out Kohlers faster than more clayey soils in other, nearby areas. I'd also do some painting and other cleanup, but the grass just won't hold off that long. Maybe next year . . . sigh.